What Challenges Do Digital Twins Solve in Construction?
[ad_1]
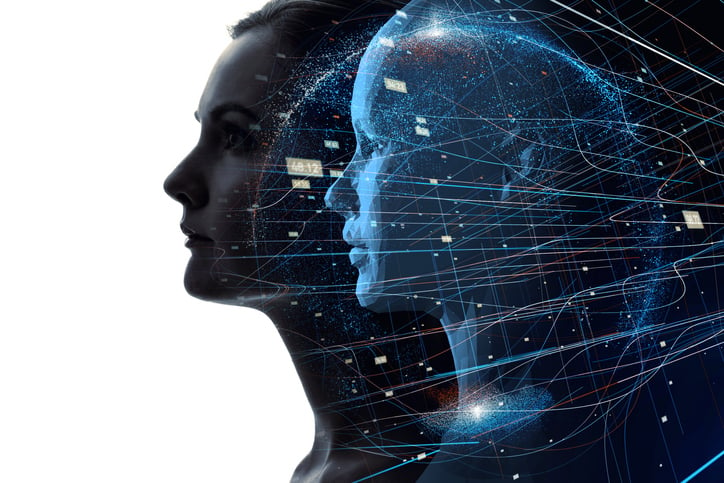
With the rise of machine learning and big data, contractors can now, more than ever, leverage data and technology to be more productive, safer, and draw insights to make smarter decisions.
Consider the words of Microsoft CEO Satya Nadella at the recent Microsoft Inspire event, when he urges companies to move beyond talking about “digital transformation” to delivering on the “digital imperative for every organization.” “Digital technology,” he remarks, “is a deflationary force in an inflationary economy. It’s the only way to navigate the headwinds we are confronting today.”
We in construction face many of the unprecedented challenges Nadella hints at and can feel them ripple through our industry: the lingering effects of a global pandemic; labor shortages, particularly among skilled trades; growing supply chain impediments for key construction materials like lumber and wood, concrete, and metal; etc. To navigate these headwinds, Nadella believes organizations across all industries must “infuse digital technology into every business process and function so that they can do more with less.” Tech-focused organizations, he believes, will have the competitive advantage to “thrive [while those that don’t] get left behind.”
One such technology concept we hear a lot in our industry, so much that it’s almost become a buzzword, is the digital twin, a piece of technology that’s expected to grow by 38% by 2026 and representing a $17.8 billion market, according to a Deloitte study.
But what is a digital twin, exactly, and what’s it all about? We’ll discuss that in this article, how the digital twin model can be used to make the largest of construction enterprises lean and agile.
What’s Inside
Digital Twin Definition: What Is a Digital Twin?
IBM defines a digital twin as “a virtual representation of an object or system that spans its lifecycle, is updated from real-time data, and uses simulation, machine learning and reasoning to help decision making.”
Meanwhile, Gartner defines it as “a digital representation of a real-world system,” used to mirror “a unique object, process, organization, person or other abstraction.” The data pulled from multiple digital twins, they contend, can be used as an aggregate data source that provides “a composite view across a number of real-world entities, such as a power plant or a city, and their related processes.”
Is digital twin a new technology?
So, is digital twin a new technology? Yes and no. While the use of digital twin technology in industry is quickly evolving, the digital twin concept has been around for many decades.
Pictured above: Mirror Worlds by David Gelernter, the first known mention of the digital twin concept (published 1991). Image Source: Available for purchase on Amazon
The earliest example of the digital twin concept put on paper was seen in David Gelernter’s 1991 publication, Mirror Worlds, positing in its abstract:
Today’s small scale software programs are about to be joined by vast public software works that will revolutionize computing and transform society as a whole. One such vast program is the “Mirror world.” Imagine looking at your computer screen and seeing reality—an image of your city, for instance, complete with moving traffic patterns, or a picture that sketches the state of an either far-flung corporation at this second […] by interacting with the images, you can interact with reality […] Indeed, Mirror worlds will revolutionize the use of computers, transforming them from (mere) handy tools to crystal balls which will allow us to see the world more vividly and see into it more deeply. Reality will be replaced gradually, piece-by-piece, by a software imitation; we will live inside the imitation; and the surprising thing is—this will be a great humanistic advance. we gain control over our world, plus a huge new measure of insight and vision.
As IBM notes, what resembled what we know now as digital twin technology was first applied by Dr. Michael Grieves in 2002 to manufacturing, announced as a digital twin software concept. John Vickers of NASA introduced the term “digital twin” in 2010. “The core idea of using digital twin as a means of studying a physical object,” IBM adds,
can actually be witnessed much earlier […] it can be rightfully said that NASA pioneered the use of digital twin technology during its space exploration missions of the 1960s, when each voyaging spacecraft was exactly replicated in an earthbound version that was used for study and simulation purposes by NASA personnel serving on flight crews.
Why Digital Twin Is Important: Benefits of Digital Twin
Bad data can cost US businesses upward of $3 trillion. Digital twinning allows you to slash those astronomical operating costs by helping you eliminate costly data inefficiencies.
Leveraging technology like Internet of Things and artificial intelligence, the purpose of digital twin technology broadly is to connect your processes and get a full view of your operations to help you work smoothly, while being agile to sudden changes through predictive recommendations.
Benefits of Digital Twin
As IBM and Autodesk highlight, there are multiple benefits to digital twin technology:
- Full view of data, eliminating data silos and “unlocking value across a product lifecycle with all historical data and real-time data in one place.”
- Smarter predictions with real-time sensor data and predictive recommendations through machine learning and artificial intelligence.
- Optimized performance through connected on and offline data.
- Better R&D, providing actionable data that can be used to make and refine products before starting production.
- Greater efficiency by mirroring and monitoring production systems and helping achieve and maintain peak efficiency throughout the manufacturing process.
- Faster results, able to mirror complex assets, factories, and processes and improve value from operations, reduce development work, and limit time to market.
- Product-end-of-life, helping manufacturers decide which products have reached the end of the product lifecycle.
Digital Twin vs Simulation: What’s the Difference?
As NetworkWorld points out, the digital twin model has often been uttered within the same breath as the term “simulation,” many using these terms interchangeably and leading to confusion over what a digital twin vs simulation is. NetworkWorld notes, while a simulation, designed in a CAD system or a similar platform (such as BIM in construction/architectural design) is typically created early in design of simulated places (i.e., not yet associated with a real, physical object), digital twin is built out of the input from IoT sensors on real equipment. In doing so, a digital twin can literally, not figuratively, replicate a real-world system—changing and adapting with that system over time, and allowing businesses to draw insights from their equipment to determine what’s working smoothly and what needs to be addressed.
What Are the Types of Digital Twin?
Most experts (e.g., IBM, Siemens, GE, etc.) agree there are 4 basic types of digital twin:
- Component twins: Component, or parts, twins represent the smallest example of a functioning component.
- Asset twins: This is the nomenclature used to describe when two or more components work together (asset). Asset twins allow you to study the interaction of the components forming this asset, creating performance data that can be processed and pored over to glean actionable insights.
- System or unit twins refer to a system or unit of different assets coming together to form an entire functioning system. System twins offer visibility to the interaction of assets and may suggest performance enhancements.
- Process twins provide a macrolevel view of how systems work together to create an entire production facility. Are all the systems synchronized and operating at peak efficiency, will delays in one system affect others?
Digital Twin Use Cases: Which Industries Are Keen to Adopt Digital Twin Technology?
There are many examples of how digital twin technology may be applied across a wide range of industries.
Examples of digital twin
- Manufacturing and automotive: Manufacturing, well equipped with automation technology and lean principles, are well prepared to pull digital twin into their stable of digital technology for better process oversight and improvement. A case study by Deloitte, in fact, revealed that, equipped with digital twin technology, manufacturing teams were able to reduce rework by 15-20%.
- Aerospace, as we discussed above, has been an early adopter of digital twinning. More recently, a survey by Business Wire (cited in challenge.org) reports that 75% of air force executives have cast a vote of confidence in favor of using digital twin.
- Supply Chain industries can use predictive digital twin technology to forecast the performance of packaging materials, and they can use digital twin models to help optimize their warehouse design and create a logistics network.
- Retail can use digital twin technology in order to generate customer modeling and simulations to better understand their customers.
- Healthcare organizations can use digital twin technology to improve operational efficiency and improve patient care through personalization.
Digital Twin: Construction Applications
The construction industry is plagued with many difficult problems. As we mentioned before, there are labor shortages, chief among them in demand skilled trades; and supply chain impediments for key construction materials including lumber and wood, concrete, and metal.
Consider of some of the key factors leading to project overruns: changes and rework; contractor financing issues; payment delays; poor cost estimation; poor tendering (bid) documents; poor material management.
Digital twins can help resolve some of construction’s biggest problems that would otherwise lead to costly construction downtime:
- Digital twin with BIM: As we previously mentioned, BIM can assist in the collaborative design process, but data captured in a digital twin during the operations phase of a project helps inform the planning and design of future projects.
- Real-time inventory management: Tool managers can create an IoT of assets via smart tools (see below) and equipment that’s tagged, asset ID tags and Bluetooth® tracking tags, GPS trackers, and other tracking hardware to better keep track of construction inventory. Construction drones, furthermore, can be used for fly-overs, the recordings providing real-time status updates.
- Smart Tools: Smart tools embedded with Bluetooth® tracking functionality can be fed into a digital twin to get better visibility to where high-value assets are; data pulled off of these assets can also be pushed into your BIM or project management software to deliver software interoperability and eliminate duplicate data, manual inputs, and mistakes; utilization data and reporting functionality can also be pulled to glean insights about tools and their continued use.
Bottom Line
Digital twin technology has come a long way since David Gelernter theorized its concept in Mirror Worlds in 1991, or NASA pioneered voyages in the 1960s. Today, as craftspeople are faced with a challenge of reinventing themselves, and the construction industry is plagued by worrying labor shortages, being data-driven, as Satya Nadella put it, is the “digital imperative for every organization,” the difference between those that thrive and those that get left behind.
[ad_2]
Source link